A Healthy Home Makeover Success Story
In August 2022, The Hansen family, Ben and Lisa, came to E3 INNOVATE as a referral from their functional medicine doctor. The family had gotten sick from mold found in a rental home they had been living in a year prior. This motivated the family to build a custom home so they could start fresh with new construction materials. Unfortunately, mold has no sympathy, and in just a few months after moving into their new place, it showed up again.
Mold doesn’t care if a house is 100-years old, or 1-year old. When the conditions are right, it can start growing 24-48 hours after a water event (1). Whether it’s hidden in the crawlspace, the attic, between the walls, in the HVAC system, or growing in plain sight around windows or air registers, mold can be found in just about any area of a home and can create a negative impact on indoor air quality and home health.
During our initial consultation with the homeowners, Ben said, “We [moved into our new home] about a year ago and thought it was safe, but recently discovered high humidity and mold.”
Microbial growth was discovered in the crawlspace of the new home, which had humidity levels as high as 90% in the summertime. As a result, humidity inside the house in the summer crept above 60%. Ben noted that moisture readings came down after the he installed a designated crawlspace dehumidifier but remained well-above the ideal range. High crawlspace humidity levels allowed mold to spread in just a short period of time.
With frustration and concern, Lisa told E3, “We need [the mold and humidity] problem in our home resolved as soon as possible so our [medical] treatment can continue and be effective rather than going backwards and getting sick again.” She was concerned for herself and her family, as they were showing symptoms of mold illness.
In addition to mold, the homeowners mentioned that the HVAC system had problems from the very beginning, and their first-year energy bills were higher than expected for a brand-new house. On top of that, Ben and Lisa were frustrated by uneven comfort; “Some rooms in our house are very hot while other rooms get much colder than the thermostat setting.”
What we found:
During the Healthy Home Assessment, E3 found high levels of particulates, carbon dioxide (CO2), and VOCs in the home, indicating a need to improve indoor air quality. High levels of CO2 and VOCs suggested a lack of ventilation and stale air. The exhaust fan in the master bathroom had a very low flow rate and the kitchen fan had no exhaust to the outdoors.
The HVAC system was oversized for the house (5-tons of capacity for 2,463 square feet (SF), or 493 SF/ton) and the air filtration was basic at best. An oversized HVAC system was contributing to the high indoor humidity levels. There was also a lack of fresh air supply; the existing design relied on infiltration as a way to bring outdoor air into the home. This is not ideal in a humid climate zone for people with mold and other environmental sensitivities because it forces a variety of pollutants into the living space in an uncontrolled way.
The crawlspace had laminate over the ground, but the foundation vents were wide open, allowing hot humid air into a cooler area. This is the perfect set up for condensation and microbial growth.
E3’s Recommended Plan:
After testing and inspecting the house, E3 compiled the data and photos and proposed a suite of home performance upgrades. The homeowners accepted and the work was soon underway.
E3’s scope of work included:
- Air sealed and re-insulated the attic
WHY: Air sealing the attic prevents particulates and dust from entering the house. It also blocks humidity and heat transfer to and from the space and results in a more comfortable, less drafty house. To do this, all of the old insulation had to be vacuumed out so air sealing could be done from the attic side.
In addition to air sealing, the bathroom fans were up graded with motion and humidity sensing Panasonic models and hard metal ducting to the roof to improve the exhaust of humidity build-up in these areas. The kitchen exhaust fan was also re-ducted to the outside.
After completing these upgrades, E3 applied a new 18" layer of blown cellulose to R-60. Burring the joists provides a continuous layer of insulation and reduces thermal bridging through the wood.
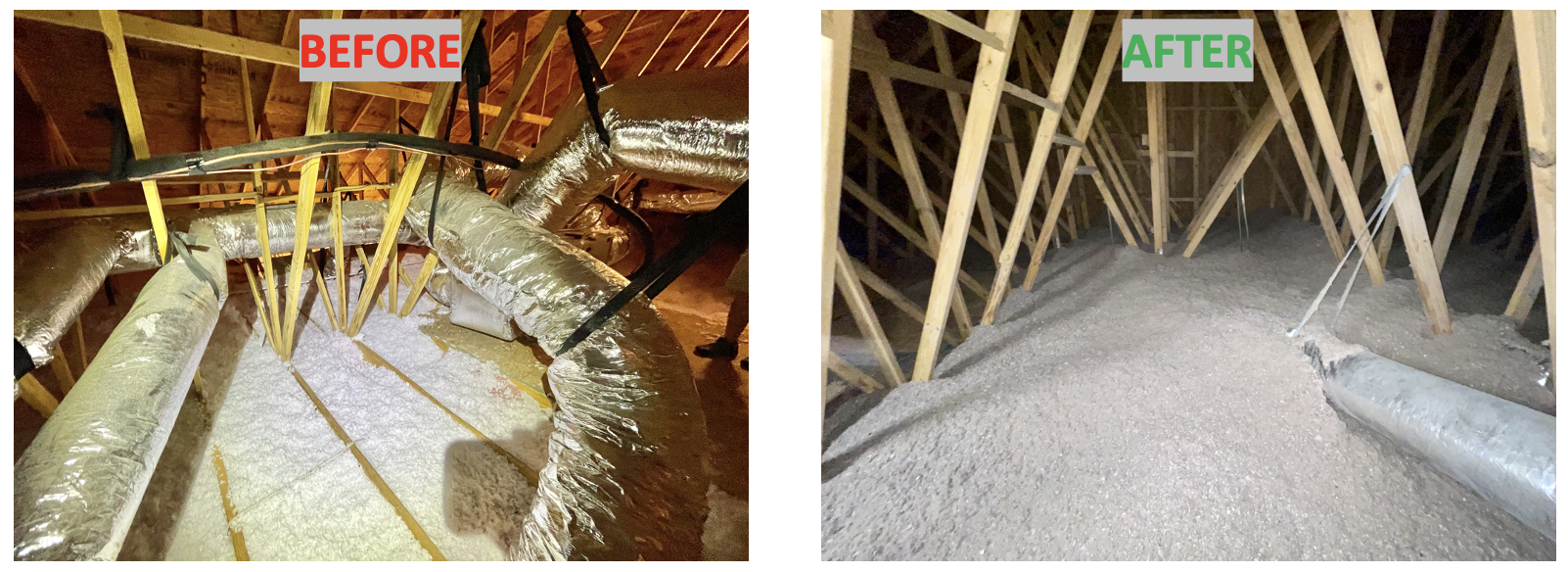
- Resized and installed a new 3-ton HVAC system and new duct work
WHY: The HVAC system was oversized to begin with, but now that the attic had been air sealed and better insulated, the existing system was 2 tons too big! An over-sized system creates short-cycling and high humidity. When systems run in short bursts, they don’t allow enough time for the air in the home to pass over the cooling coil to dehumidify. The air will feel cool, but clammy. By reducing the size to 3-tons and adding variable speed capacity, the system can now match the load in a wider range of indoor conditions. Doing so also increases the efficiency to 821 SF/ton.
Rather than using one system to serve all the needs of the home, E3 installed a Mitsubishi system with one 2.5 ton central air handler and one 1/2 ton designated mini split for the master suite. Because of the layout of the house, the heating and cooling needs for the master area were different than the rest of the house. Using a separate system provides more control and consistent temperatures in the space.
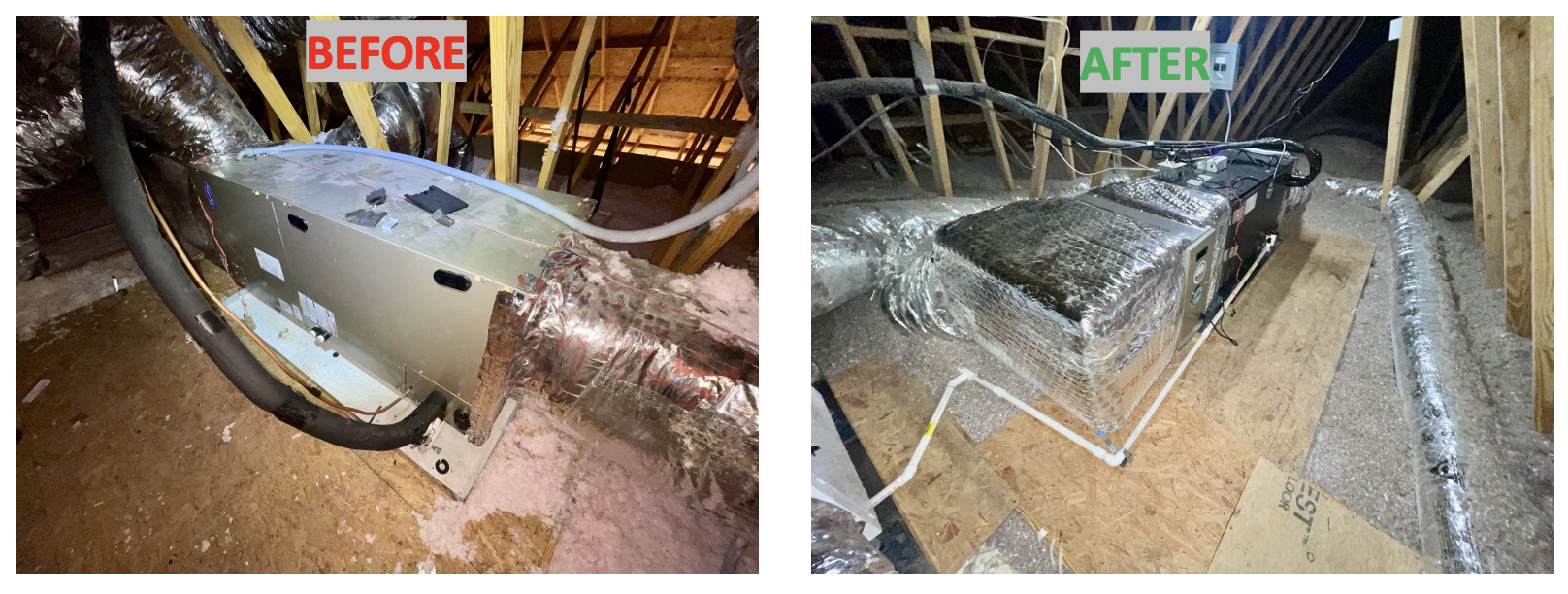
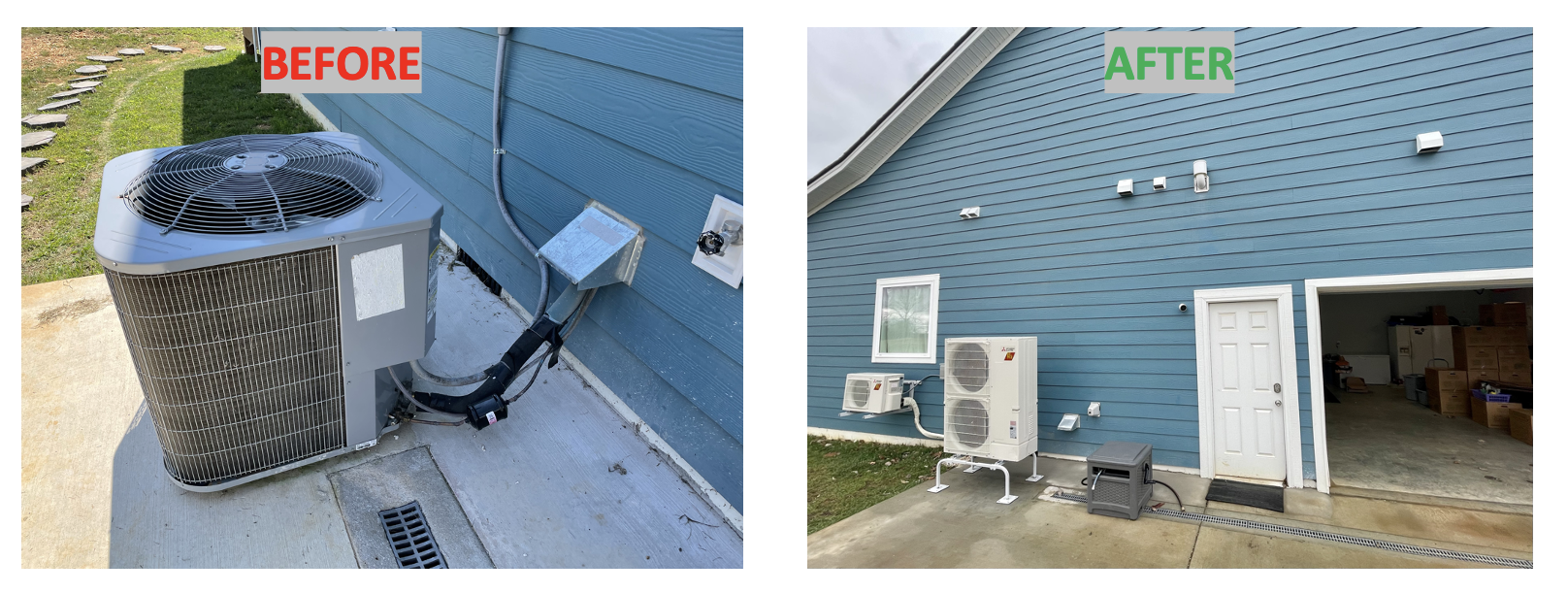
- Installed new duct work
WHY: The original HVAC system was oversized. This made the ductwork too big for the new smaller system. In addition to making the ductwork smaller, it was buried under the attic insulation to help insulate it and save energy.
- Added a PureAir Filtration box and UV-C light to the HVAC system
WHY: Additional filtration will help the homeowners keep the air inside the house clean and prevent dust. The UV-C light keeps the coils of the HVAC system clean and prevents microbial growth inside the unit.
- Added a whole-house dehumidification system
WHY: A proper sized HVAC system will work to keep the house dry, but in the shoulder months (spring and fall) when there isn’t as much need for cooling, the dehumidifier will take care of the latent load (i.e. the humidity that accumulates indoors).
- Added a Panasonic ERV with a Fanteck pre-filter
WHY: The ERV brings in a supply of fresh air from the outdoors. Fresh air is important for optimal health, and it helps to dilute contaminants like CO2, chemicals, radon, and cooking odors. The pre-filter helps capture more of the outdoor contaminants like mold spores, pollen, and even small bugs that can get into the ERV unit.
- Installed an E3 Sealed Crawlspace system
WHY: This system, which includes a sealed vapor barrier, spray foam in the rim band, and a clear termite viewing strip, will help prevent moisture from coming in through the ground and provide a clean barrier from the soil. It also improves indoor air quality in the home, since about 40% of indoor air comes up from the base of the house.
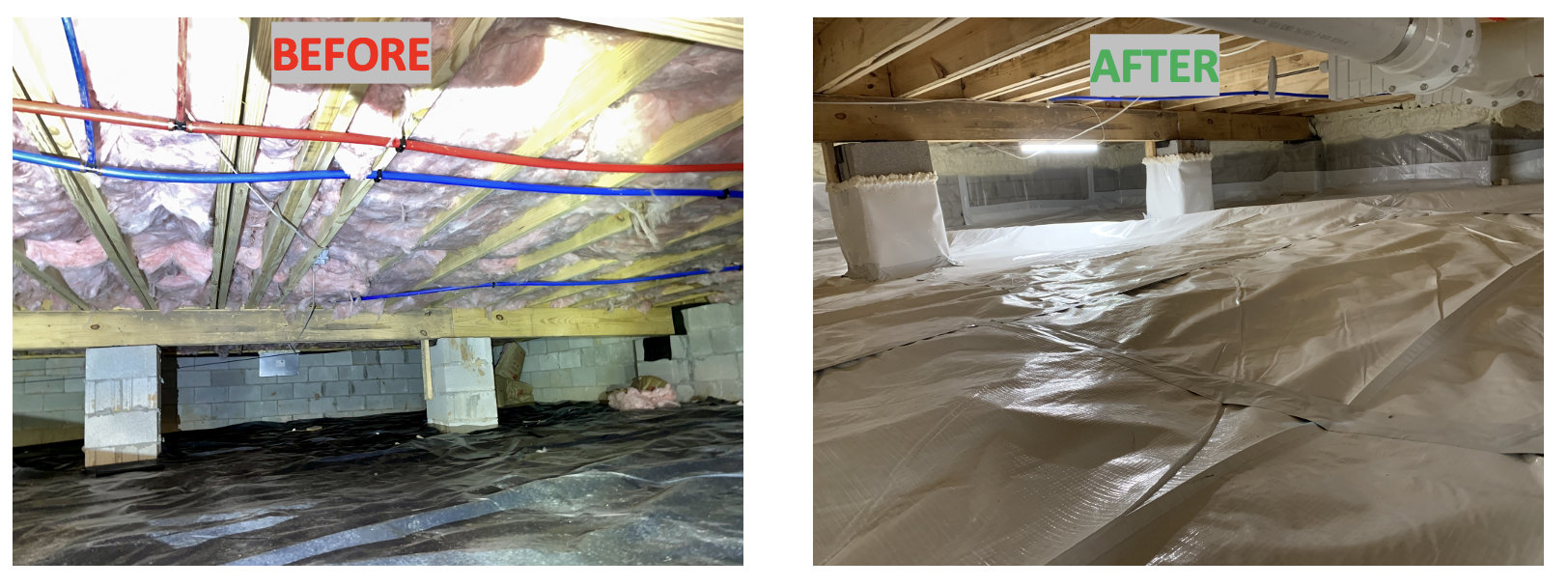
- Upgraded the crawlspace dehumidifier to an UltraAire 98H
WHY: Adding an extra layer of dehumidification to the crawlspace helps keep the space dry and prevents future mold growth. Adding ductwork improves the circulation of dry air.
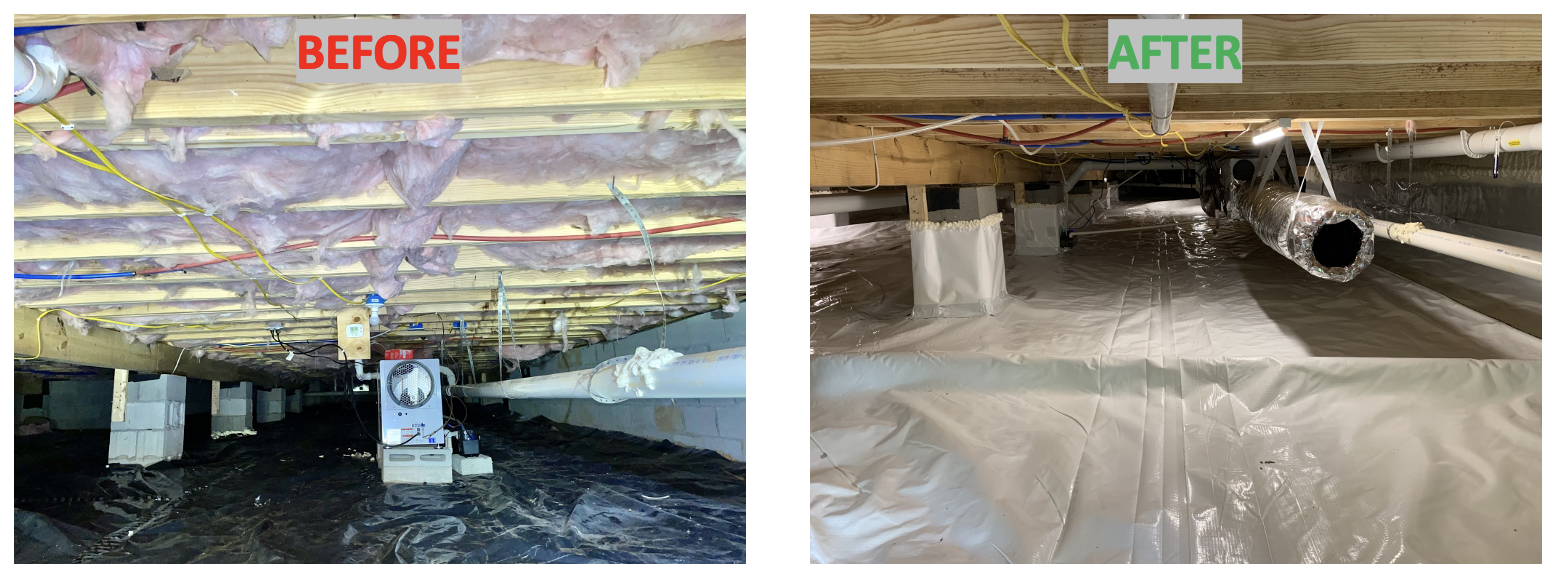
- Installed a more robust radon mitigation system
WHY: The existing radon system included one central inlet pipe located above a moisture barrier. This can be 'ok' when radon levels are low to begin with and there isn’t a concern for moisture and air quality. Because radon systems can exhaust soil odors and moisture in addition to radon, E3 upgraded the mitigation system. A black perforated pipe was laid out in a snake-like path over the soil before the laminate was installed. This helps remove the soil odors, moisture, and radon before it has a chance of even getting into the crawlspace. Because there were multiple arms of perforated piping, gate valves were installed to control the flow in each branch.
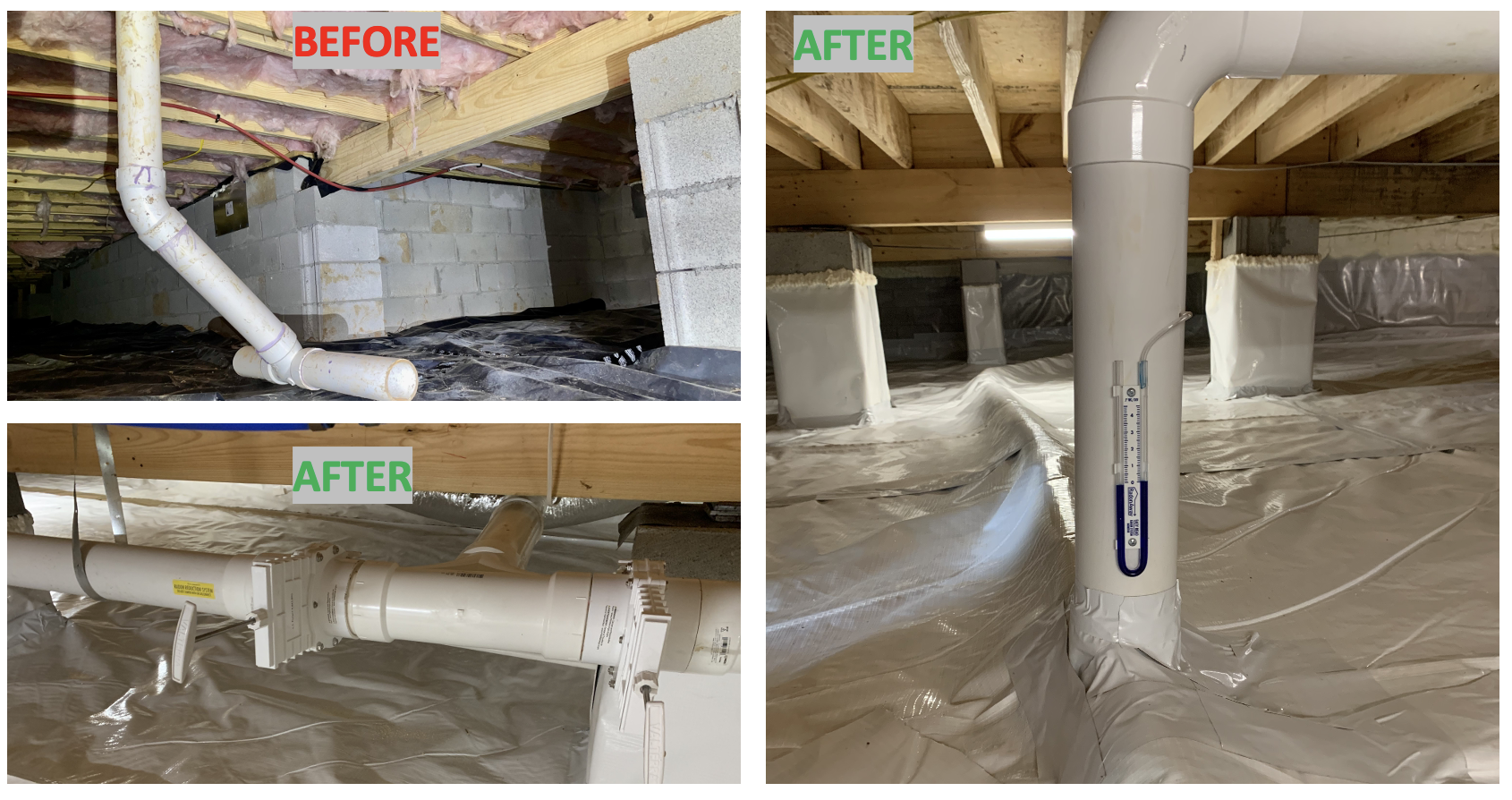
Results
After completing the work, indoor air quality improved and the homeowners felt more comfortable in their house. Success! Particulate readings, chemicals, and CO2 levels were all reduced. Lisa also reported an overall improvement in the health of her family.

Particulates, chemical VOCs, and CO2 were all significantly reduced. Chemical exposure was still elevated when we did our post testing in April of 2023; we anticipate this is from consumer products that the homeowners are still using that emit VOCs, such as personal care and cleaning products. However, we are pleased to see this air pollutant reduced by 300%.
Now that the Hansen’s have a healthy home, they realized how important maintenance will be to keep the systems working at peak performance. They opted in to E3’s home maintenance program and have E3’s experienced technicians service and clean all of the systems in their home twice a year.
We understand how frustrating having to make this kind of investment can be, especially after just completing the construction of a new home. That is why we highly encourage having an expert on your construction team who can plan out the details of a high performance home and who understands the WHY behind certain elements of the design. We are happy to have solved the Hansen’s air quality and comfort concerns and we hope their home can provide a health haven for years to come.
SOURCES
(1) https://www.epa.gov/mold/ten-things-you-should-know-about-mold