Starting the design of a new custom home can be exciting and daunting at the same time. Planning the layout, envisioning the view from the kitchen, and deciding where to put the solar panels are probably everyone’s favorite parts about building a custom high performance home. But when it comes down to the guts of the house and how to make all the details come together to create an ultra-efficient solar-ready house, things can get a little confusing.
Last year, the Phil and Erica reached out to E3 INNOVATE with a vision of building a net-zero energy house. A net-zero energy home is one that produces as much energy on-site as it consumes in one year. Typically, this is accomplished by building a super energy-efficient home and then off-setting the rest of the electricity demand with a grid-tied solar PV system installed either on the roof of the house or on the ground where sun exposure can be optimized. The key to building a net-zero energy house is first reducing electricity demand as much as possible.
The family wanted to know how to turn their vision into reality and what key components were needed to get there. So, they hired E3 to help them find answers. E3 started by developing a building energy model to optimize efficiency while also staying on a budget. The model helped find the right combination of insulation products, window properties, and other features of the home. Next, E3 completed a Manual J, S, and D, which allowed us to design an HVAC system that met the predicted heating, cooling, and dehumidification needs of the house. With this exercise, E3 was able to design an ultra-efficient mini-split system that served the home with just one outdoor compressor unit.
The modeling showed that a combination of sprayfoam on the roof deck and in the vaulted areas combined with wet-blown cellulose in the wall cavities would provide the necessary R-value and be more cost-effective than a fully foamed house. Additional air sealing details would also reduce the air leakage of the shell of the house.
Other features of the home include:
ERV: Because we anticipate the house to have an air leakage rate of around 1 ACH, an energy recovery ventilator (ERV) was included to provide the right amount of fresh air to keep the space healthy and to flush out air pollutants that accumulate indoors. An ERV pre-conditions the incoming air with the outgoing exhaust air that is pulled out of the home at the same rate.
Smart Bathroom Fans: Bath fans were ducted straight out of the house with hard metal ducting to create optimal air flow. The “smart” features include a humidity and motion sensor that automatically turns the fan on and off depending on the needs and use of the space.
Heat Pump Water Heater: A heat pump water heater takes heat from a room and pumps it into the water. Remember Law of Conservation of Energy? Energy is never created or destroyed; it’s transformed! Heat pump water heaters are very efficient and eliminate the need for natural gas.
Designated Dehumidifier: This system will help keep the basement dry as moisture migrates through the foundation walls. This is a long-term solution to mitigate moisture and mold growth.
Multi-zone Heating and Cooling System: The multi-zone compressor works to serve three zones in the home. Refrigerant lines feed a mini-split wall cassette unit in the basement and in the loft area on the third floor and a high static-pressure ducted system that serves the main floor. Fancy and efficient!
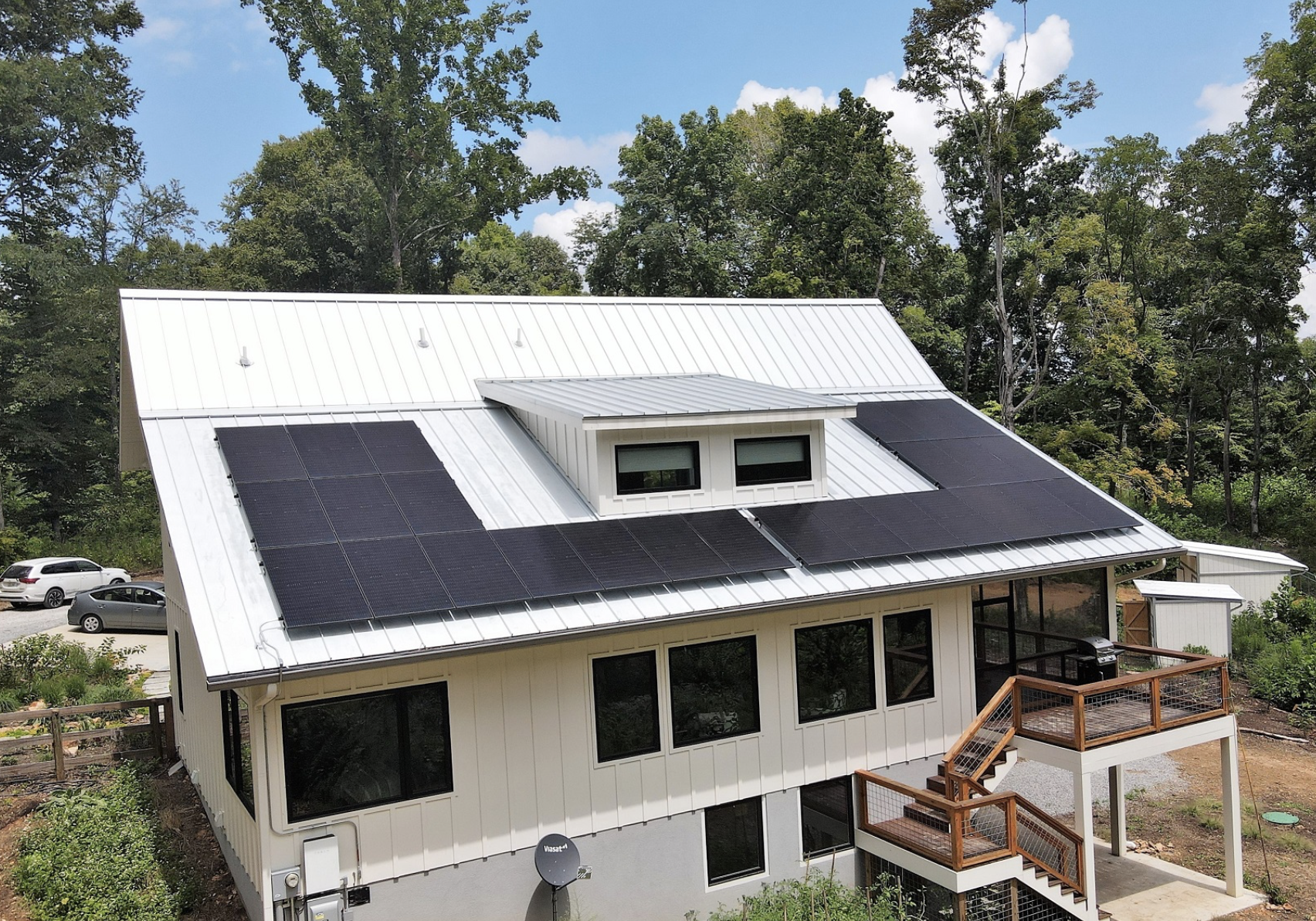
In addition to designing and selecting the mechanical equipment, the homeowners contract with E3 EcoWorks for the installation of these systems plus the insulation and air sealing details. During the construction process, E3 provided pre drywall testing to ensure all of the air gaps were sealed. With the pressure test running, we were able to hit all the minor gaps and cracks with caulk and foam to reduce the air leakage rate even more! This step helps prevent moisture issues in wall cavities. The overall tightness (aka air leakage rate) of the home at the end of construction came in at 1.14 air changes per hour (ACH50).
The homeowners’ goal was to get as close to zero-energy as they could, relying as little on the utility as possible. So, after construction, the homeowners installed a 10 kW roof-top solar array and two Tesla Powerwalls. In the end, this solar array provided enough electricity to power the home for about 90% of the year. If they are so inclined, Phil and Erica could add more solar panels in the future to get them to a true net-zero.
At the end of the project, E3 completed a Home Energy Rating Score (or HERS index), which provides a summary of the energy savings and a score depicting consumption compared to typical homes. The HERS index for this home with the solar array is a 10, meaning that it uses 90% less energy than a standard existing home (score of 100). For reference, most newer homes in Middle TN have an air leakage rate between 5 and 7 ACH and a HERS index between 65 and 70.
E3 was Phil and Erica’s go-to expert for all of the elements of their high-performance house and worked with Lightwave Solar in Nashville for the solar components.
Check out the video here!
Are you building a custom home and want to make it a high-performance healthy home? Give us a call today and talk to one of our building scientist to see how we can help you turn your dreams into reality.